;
;
;
Next Article
Spring: enjoy the fresh air while you can
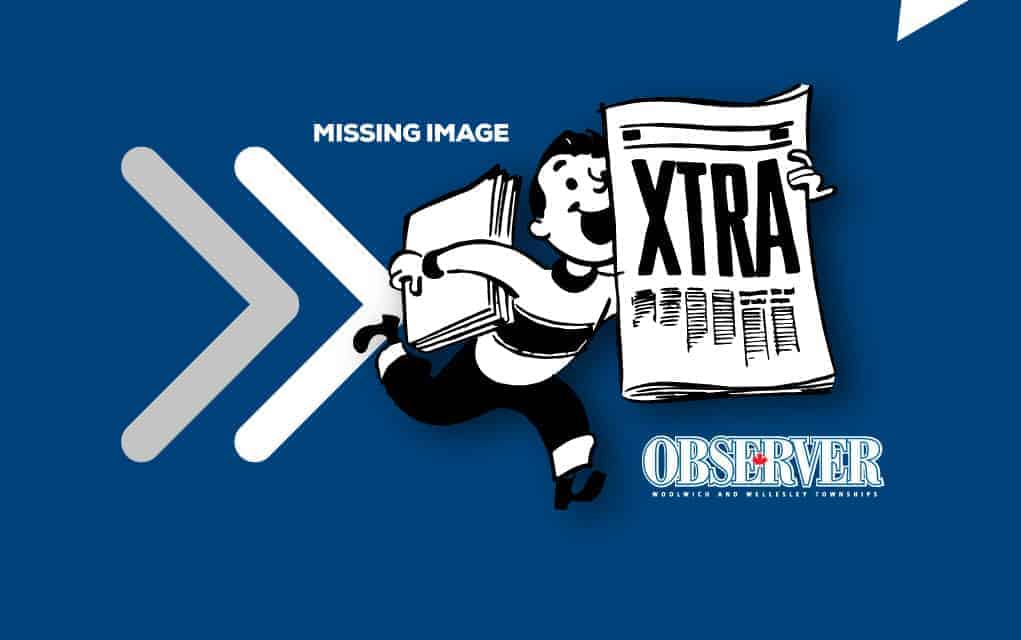
The winter Bill Cassel was nine, he got sick and wasn’t allowed to leave the house for three months. “If you think you’re going to sit around and drive me crazy, you can think again,” his mother told him. “When you get back outside, you’re going to need socks, so you may as well learn […]
Last updated on May 04, 23
Posted on Mar 12, 10
3 min read